There are no known human limits when it comes to the causes of "spaghetti syndrome",…
How to take your cable management in solar installations to the next level
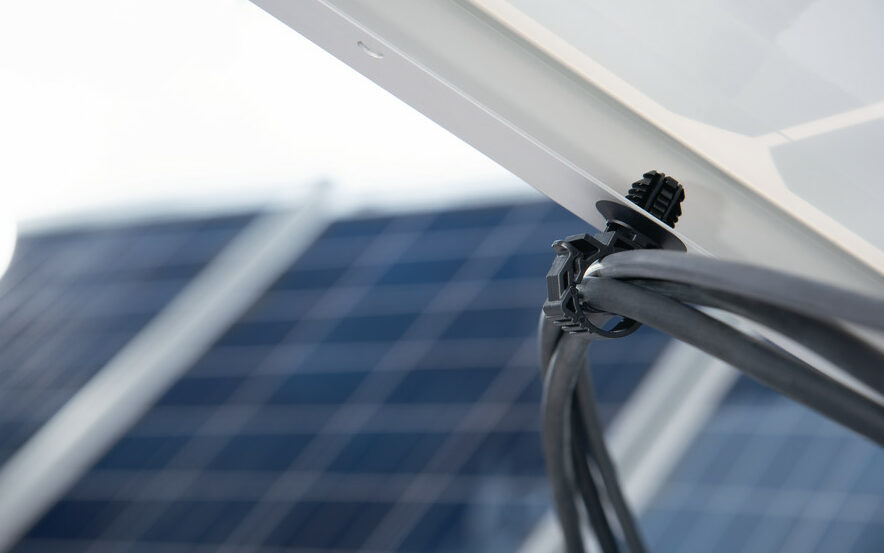
In addition to facing harsh weather conditions, solar plant components must also endure other challenges. These include poor application of wire and cable management as well as a missing maintenance strategy, which can be catastrophic to the performance of the entire solar plant.
But in contrast to high temperatures, storms, and natural disasters, problems with cable management in solar installations are both predictable and easily avoidable. Getting on top of these issues helps this renewable energy source to grow economically. In Brazil, for example, forecasts indicate that the number of installed solar energy systems should reach 800,000 by 2024.
According to Nick Korth, HellermannTyton product marketing manager for the energy sector in the Americas, there are two steps you need to follow if you want to reduce risk and additional costs.
The first is to meet all the requirements of national and international rules and standards. But, according to Nick Korth, “these standards only provide a basis for evaluating and inspecting solar systems; they do not guarantee a long life cycle for the systems. Accordingly, the second step must be to find best practices and implement quality assurance programs that will guarantee the performance of the installation.”
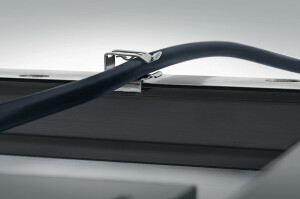
As an example, he points to the damage caused to cable jackets by the misapplication of metal clips. Korth says that it is not uncommon to see workers hitting cheap, poorly designed metal clips with the back of a pair of pliers or screwdriver. This not only distorts the clip, which affects performance, but can also cause damage to the solar module itself.
The solution is to use good quality metal clips that are designed to be installed easily and efficiently, such as the EdgeClip range. These stainless steel EdgeClips are ideal for this task. Not only are they resistant to UV radiation, temperature changes and weather-induced chemical reactions, they also prevent photovoltaic cables from bending and being damaged, which avoids short circuits.
The importance of using the right products
A good cable management plan requires dependence on the right materials and in the perfect product for your specific application. Plastic products are generally not suitable for the solar industry and are often considered as an lower quality alternative to metal. But as with all products, quality depends on the material and the manufacturer, as not all plastic wire and cable management products are designed and manufactured the same way. Don’t let the perception of supposedly inferior plastic products keep you from looking for and using a stronger, well-made, longer-lasting plastic cable tie.
As confirmation of the need to invest in better quality products, Nick Korth refers to a case where a solar farm was installed in a desert environment, using cheap “UV-resistant” cable ties on the solar panel. After replacing them three times in four years, the owner of the plant decided that he was fed up with the compromises: he went to the market and found products that could withstand constant heat, thermal changes, wind and sun – he turned to solutions from HellermannTyton.
“Let’s break down the math,” Korth says. “Employing four workers for five days at $20 per hour adds up to $3,200 per year. Over five years, the solar system owner would spend $16,000 just to replace cheap clamps, a significant increase of operating costs. In addition, there is the high risk of several failures due to stress on the conductors.”

Solar industry EdgeClips with Cable ties from HellermannTyton are equipped with UV stabilizers and allow the installation of photovoltaic cables, with or without predefined holes. HellermannTyton plastic clips for solar applications are manufactured with combined materials for different regions and environmental conditions, using the highest quality materials to meet the requirements of the solar industry. They provide secure anchoring of photovoltaic cables and are available in a variety of materials, sizes and tensile strengths to suit any solar application.
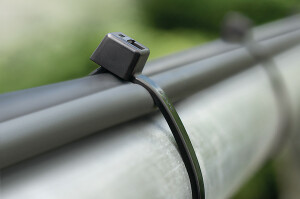
“Our solar solutions, made from UV-resistant polyamide 11, last five to seven times longer than a standard solar clamp with a UV rating. Parts made from UV-stabilised plastic, along with other stabilisers, can significantly increase the lifespan of these products. In fact, some plastic compounds can last 15 to 25 years. Choosing engineering plastics designed to perform in the solar components will certainly pay off,” says Korth.
The right solution for your application
Solar solutions from HellermannTyton are as versatile as the different regions and areas of application themselves. When searching for the perfect product, personal consultation is the best way to go. The experts at HellermannTyton are happy to help you find the right product and drastically reduce your overall costs in the long run as a result. Get in contact here.
2021 marks the 20th anniversary of the EdgeClip family
Whether solar, automotive or any other industry: For already 20 years, customers from a wide range of industries have been relying on the versatile EdgeClip product range. Today, the practical clips for edge fastening are available in over 300 variants, made of more than 100 different material combinations.
Learn more about the EdgeClip family here.
#4799