In addition to facing harsh weather conditions, solar plant components must also endure other challenges.…
Cable and fluid management in vehicle construction: What you need to know about future trends
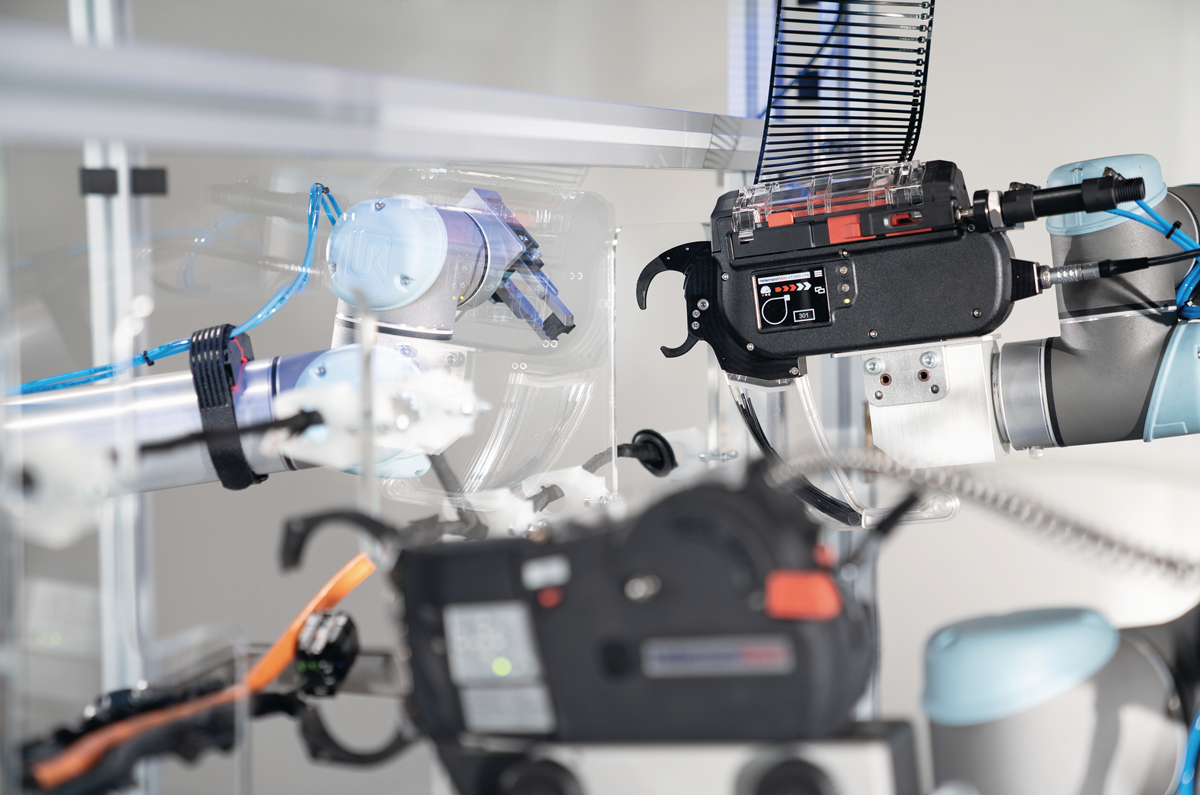
In the grand scheme of vehicle design, wire and fluid management have often been treated as an afterthought. But the rapid transition from combustion engines to electric drive trains is forcing a rethink. Product managers and engineers are now having to look earlier for solutions to wire and fluid challenges. But, this early in the game, there are still many approaches and few standards. And that’s where HellermannTyton is pioneering some interesting approaches to cost optimisation of fastening elements.
The electric vehicle (EV) market is mushrooming, with projections suggesting that in only ten years’ time, around half of all the new cars sold will be fully electric. The speed of that shift to high-voltage systems, coupled with an increasing array of sensors, is making an earlier and more systematic approach to harness fastening and routing in the vehicle architecture inevitable.
Although the challenges for product managers and engineers are not new, they are throwing up new hurdles: space utilisation, electromagnetic interference, vibration noise, weight optimisation, thermal management and automated harness production. Practicable solutions to the points of detail that keep them up at night are often found at the nexus of collaboration with external cable management specialists.
One size doesn’t fit all
Although the technological challenges are universal, OEMs are pursuing different philosophies regarding their platform architecture. Consequently, today’s fastening components must check off many boxes – minimal weight, cost control, flexible routing orientation, easy insertion combined with high extraction force, simple or pre-assembly, impact resistance, high and low temperatures, UV and chemical resistance, and not least, scalability.
As a collaborative partner to OEMs and first tier suppliers, HellermannTyton’s short-term role is to facilitate the development of cost-effective bundling and fixing parts in a given architecture. But beyond that, according to Harald Gottlieb, Vice President Automotive at HellermannTyton, the company’s aspiration is to provide innovative component solutions that minimise assembly costs across different platforms.
That means keeping an eye open for the commonalities across a range of isolated part development projects with similar briefs. And then evolving standardised approaches wherever possible. It’s an exciting time which calls for a lot of imagination, inventiveness and ultimately good working relationships with the customer base.
Getting a grip on thermal management
Higher voltages and bigger battery packs require active cooling at the charging inlet. So, the fastening of fluid pipes for optimal thermal management is taking on new significance in the EV context. Welding on custom fasteners consumes a lot of process time and effort. To turn that around, HellermannTyton has returned to the drawing board and factored in all the requirements for more efficient assembly. The result is Soft Grip, a fixing tie designed to save time, money and development effort around fluid management.
This unique twin-shot fixing tie is easily adaptable to a range of application requirements. It is injection moulded from heat-stabilised PA66HS with a soft TPE inner layer. It grips hoses and wires without damaging them, inhibits lateral and rotational movement on smooth bundles, and suppresses vibration rattling. The tie head slots into a variety of different mount configurations. In this way, one Soft Grip fixing tie can replace a variety of p-clip diameters and also reduce the need for lots of bespoke fasteners. The foot part and the mount geometry can be easily adjusted to fit individual requirements, making it a highly versatile, cost-effective, and scalable part solution.
Moving towards standardised HV clips
Different high voltage routing preferences from manufacturer to manufacturer are also turning out a variety of specific requirements, like conductor spacing and material expectations. These currently preclude off-the-shelf solutions.
The building block approach that HellermannTyton has applied to the Soft Grip mounts also translates well to HV clips and clamps. It ensures that moulds can be easily reconfigured for a variety of mounting options and geometries without having to start the design and tooling from scratch.
Collaboration with experienced fastening designers who have this mindset helps OEMs to achieve optimal design and cost-efficiency. For example, we view each HV clip that we develop from all perspectives, including ease of assembly, reliability and scalability across many platforms.
Already, automotive customers are benefiting from our insights gained in aerospace part development. These help us strike the right balance between component weight, size, durability and temperature performance.
Automation of harness production
Looking to the road ahead, the good news is that HV wiring systems, and especially flat busbar conductors, are relatively simple constructs with few branches. This not only simplifies their manual pre-fabrication but also brings us a step closer to the automated application of fasteners.
There is already a broad portfolio of clips that can be applied to round cables by HellermannTyton bundling tools. Needless to say, we are already testing the automated application of clips to busbars for OEMs using these ‘Autotools’. See the main picture, above.
Turning our attention to the electronically governed systems hidden behind the outer skin of a vehicle like radar, LiDAR, cameras and sensors, we believe that automated bundling will become a necessity for assuring and documenting all harness parts involved in connecting the dozens of low-voltage electrical components – especially those employed in redundant systems. Those connections aren’t just simple low-voltage wires any longer. They are increasingly coax or high-speed data cables that require bundling with repeatedly precise and traceable tension forces.
Watch this video to see Autotools in action bundling clips to part of a wire harness.
The parts for today’s EVs need to lay the foundation for facilitating scalability in mass production. OEMs won’t be making the vehicles bigger to accommodate added technology, and they must continue to seek ways to decrease weight, add range and maximise cargo volume. The best recipe for that ideal result isn’t always right in front of us. But together, we’re discovering which ingredients and which new method is right to route, protect and mount all those connections and reduce weight further.
One size may never fit all, but we can certainly do a lot to reduce overheads with a common approach based on experience, rather than a piecemeal approach targeted at isolated architecture preferences.
#4964