For people, by people. What often sounds like a hollow phrase is a tangible part…
Two in one: how a new diesel resistant and halogen free marker helps a locomotive manufacturer increase safety
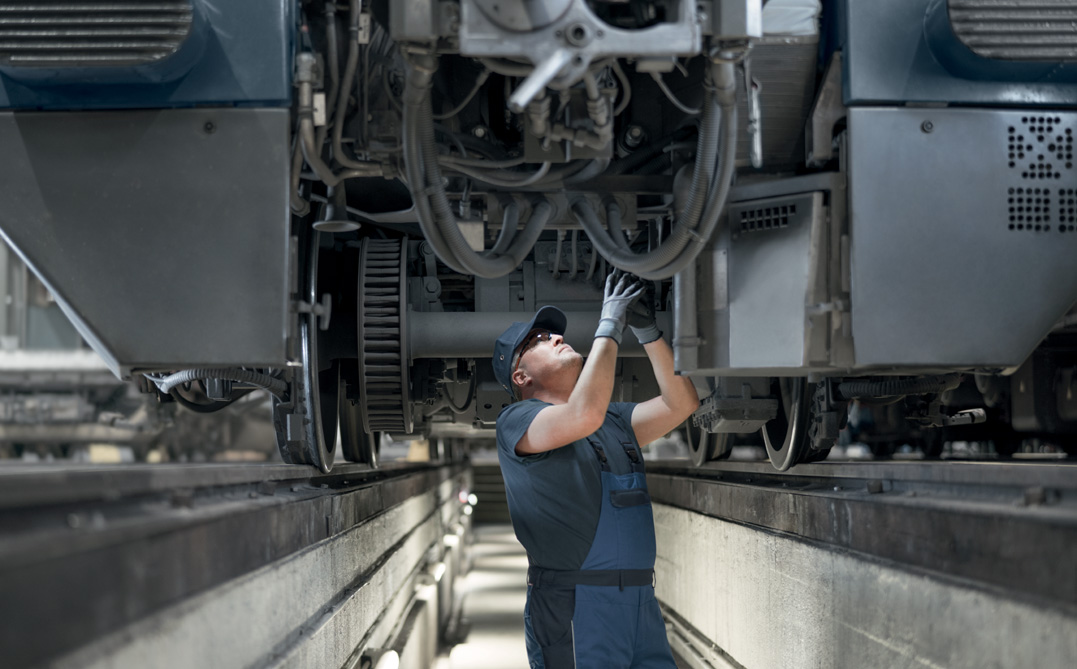
The mistakes of the past have taught us that fire protection in the rail transport sector is a very serious concern. Legislators and standardisation bodies have defined strict requirements for the components in rail vehicles. The highest demands are placed on the safety of passengers in the event of a rescue from a long tunnel. However, the fulfilment of these standards is often challenging for manufacturers of locomotives. A new HellermannTyton product ensures safe and efficient labelling in the railway industry.
Components around the electrical wiring in railway vehicles are subject to different standards specifications. The European Railway Standard EN 45545-2:2016 (specifications R22/R23) and the requirements of EN 50343:2014 (annex H) are the main standards in the railway industry.
Reduction in part diversity and the reduction of the cost of economic sanctions
“Engineers in the rail industry increasingly work to global scenarios where rail vehicles are deployed across the borders of countries and legislation”, explains Nadine Hansen, Category Manager for Identification Products at HellermannTyton. The dilemma is posed by the ever-increasing global nature of the business: “With regards to identification with printed markers in ladder format, the two standards have so far been served by two different materials,” says Nadine Hansen. “Now the market is clearly signalling that both requirements need to be met in a single product.” Customers producing diesels engines, for example, are increasingly seeking markers that are not only diesel resistant but also halogen free.
A reduction in part diversity and the reduction of the cost of economic sanctions in the event of non-achievement of the standard requirements are behind the trend.
Passing several tests with one heat shrink material is like searching for the Holy Grail
“We were in the process of testing a new double-sided printable and halogen-free shrink material as the first request from a major European rail vehicle manufacturer came in,” recalls Technical Project Manager Marco Schaffer. “Keeping the material flexible whilst preserving the resistance to liquids was the crux of the issue. At times it seemed that passing several tests with a single heat shrink material was like the quest for the Holy Grail.”
“Weeks later, when the first positive results finally arrived from the lab, everyone involved was very excited”, remembers Nadine Hansen.
The TLFD DS product not only attained hazard levels 1 and 2 of the EN 45545-2:2016 specifications, but also the highest hazard level 3 in all test results. Due to the special composition of the polyolefin material, TLFD DS helps minimise the risk to life in the event of a fire. It generates little smoke, does not consume oxygen or form toxic gases. What’s more, TLFD DS also remains resistant to liquids such as diesel or oils.
MADE FOR RAIL: Safety. All the way down the line.
For over 50 years we’ve been manufacturing and supplying cable management products that conform to European rail standards. Watch the video to see how we help our rail customers stay on track.
Why HellermannTyton is MADE FOR RAIL. Click here to watch the video:
One thing leads to another
“In the feedback discussion with the customer, we discovered that what they ideally wanted was not just the new product but also a complete solution”, recalls Schaffer. A reduction in the total cost of expenditure for the labelling of diesel locomotives was suddenly on the table.
“None of us could have predicted a year ago that the fulfilment of a product request would lead to a complete changeover of the customer’s printing centre at the locomotive factory in Germany,” says Hansen. The order included 10 printer systems that produce up to 20 000 markers a day plus the training of three employees with the new software and service agreements ensuring continual productivity.
“Close partnership was crucial,” says Nadine Hansen. “Through tight collaboration of expertise we were able to fulfil all the customer’s requirements.” The combination of high performance printer hardware, flexible software, training and a service level that even included customisation of the printer drivers sealed the success of the project.
The customer is so satisfied with the amount of service and consultancy that they also now work with us on all other identification materials, including labels.
What does the future look like with the new material?
This project example shows that when it comes to savings potential in rail vehicle construction, it can be worthwhile to start small and think big. The customer can rely on certified products and on-site service, based on our industry know-how.
Experience from customer projects such as this one flows into the solution of other challenges related to industrial marking.
“We are working on an extended range of products with this excellent material,” Nadine Hansen adds. “Other industries that place high demands on the low flammability and high fluid resistance of shrink materials will also benefit from our TLFD DS development.
TLFD DS heat shrink marker characteristics at a glance:
- conforms to EN 45545 and EN 50343
- halogen free, cross-linked polyolefin (PO-X) with a 2:1 shrink rate
- fluid resistant (diesel and oils)
- shrink temperature +120°C, operating temperature range -55°C up to +125°
- ladder format, suitable for double-sided thermal transfer printing
- 9 sizes for diameters from 38.1 mm to 1.2 mm
- 50 mm and 25 mm cut lengths – other sizes available on request
- standard yellow and white colours
Further details about HellermannTyton products that meet the European Railway Standard EN 45545-2:2016 are available here: https://www.hellermanntyton.com/markets-and-industries/cable-marking-rail-industry#tab1
Do you have any feedback about identification projects where finding materials that meet standards specifications is a challenge? We’d love to hear from you.
#3436